New Biomaterial Could Save Our Oceans From Plastic Pollution
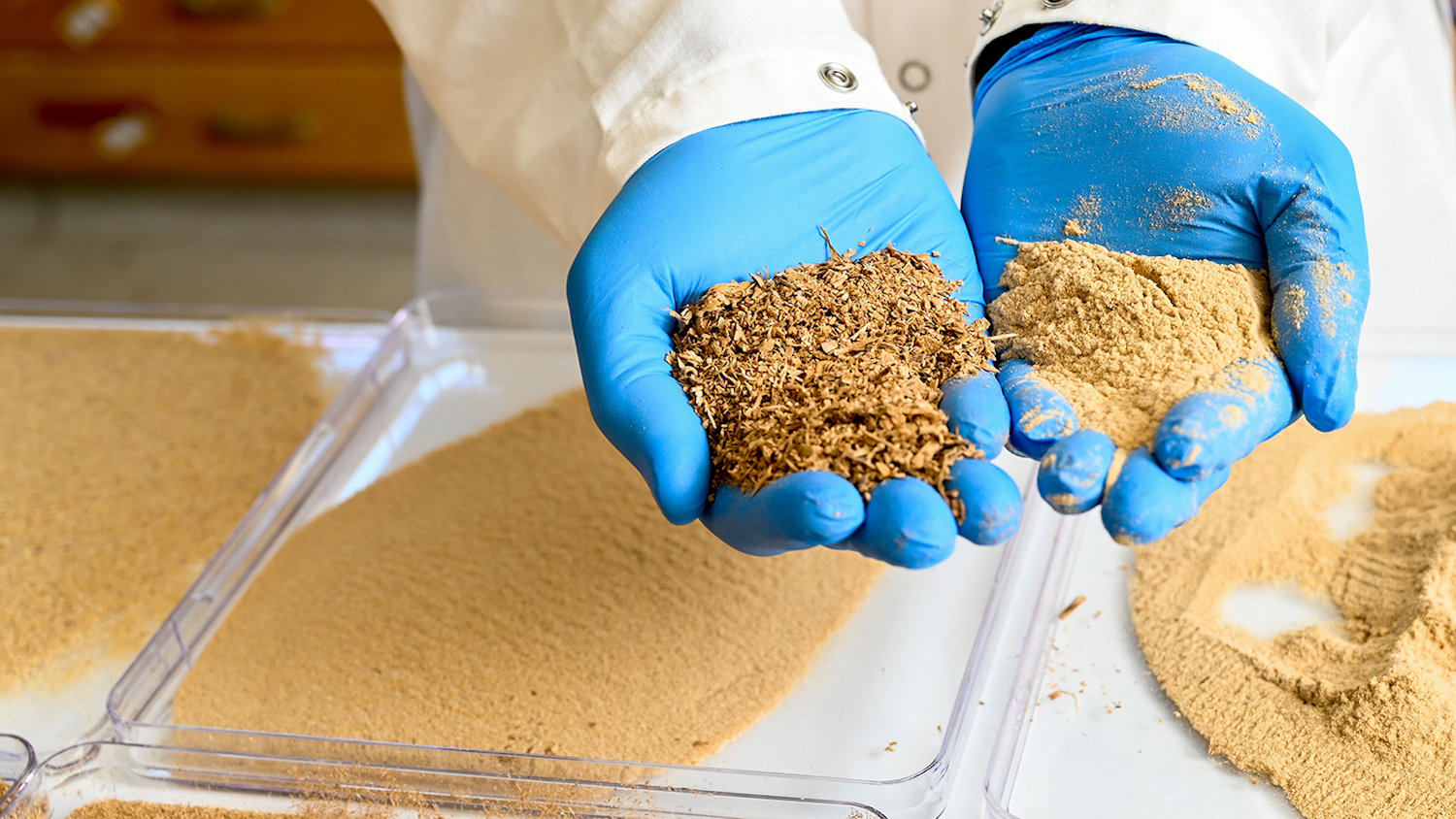
Straws, water bottles, shopping bags, cups, utensils: so many of these everyday items are made from single-use plastics, meaning they’re used just once and then thrown away. As a result, these items often end up in landfills and waterways, where they not only choke and ensnare wildlife but also leach harmful toxins into the environment as they decompose.
Now researchers at NC State have developed a new biomaterial that could help solve the worsening problem of plastic pollution. Lokendra Pal and Lucian Lucia, professors in the Department of Forest Biomaterials, have discovered how to convert leftover sawdust powder and agro-residues into a Styrofoam-like packaging material.
The wood-based material could someday replace the plastics found in many single-use items. With support from the Chancellor’s Innovation Fund, Pal and Lucia are currently conducting pilot trials, in advance of testing and commercialization by potential industry partners. They’re mostly focused on manufacturing packaging and food service products.
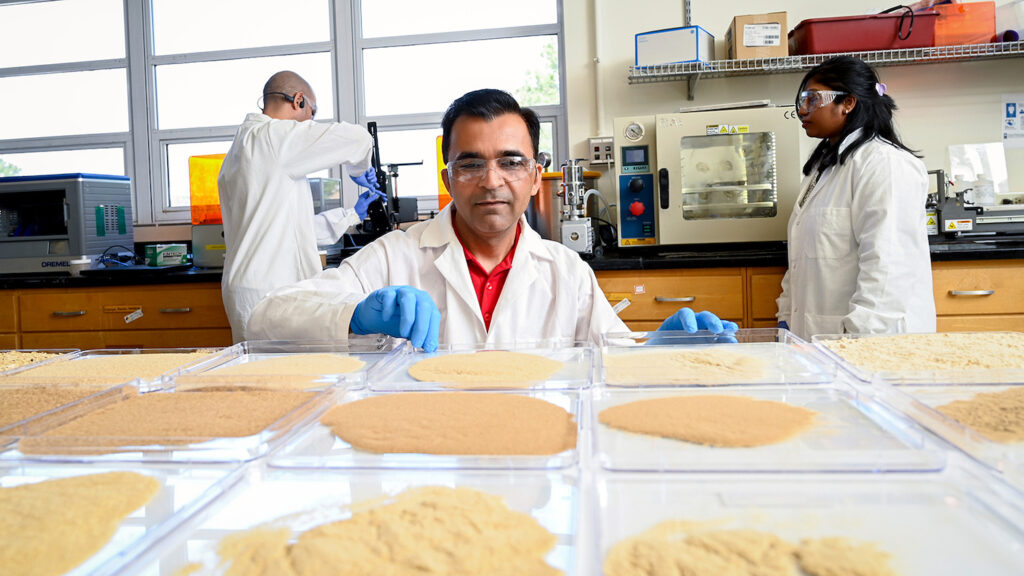
Packaging and food service products are often made from Styrofoam, a popular brand name of polystyrene, which is a petroleum-based plastic. Because Styrofoam is non-recyclable and non-biodegradable, these products are quickly discarded and make their way into landfills and waterways, where they can take 500 years to decompose.
“Items made from Styrofoam aren’t used very long before they’re discarded. But they pose a major threat to human and ecosystem health,” Pal said. “The lightweight composition and buoyancy of Styrofoam allows it to float for long distances in water. It also can absorb and transport toxic pollutants, such as mercury.”
Over 300 million tons of plastic are produced every year, half of which is used in single-use items. Research shows that an estimated 12 million tons of that waste enters the ocean every year. Unfortunately, if plastic production and disposal continue at current rates, that amount will nearly triple to 30 million tons per year by 2040.
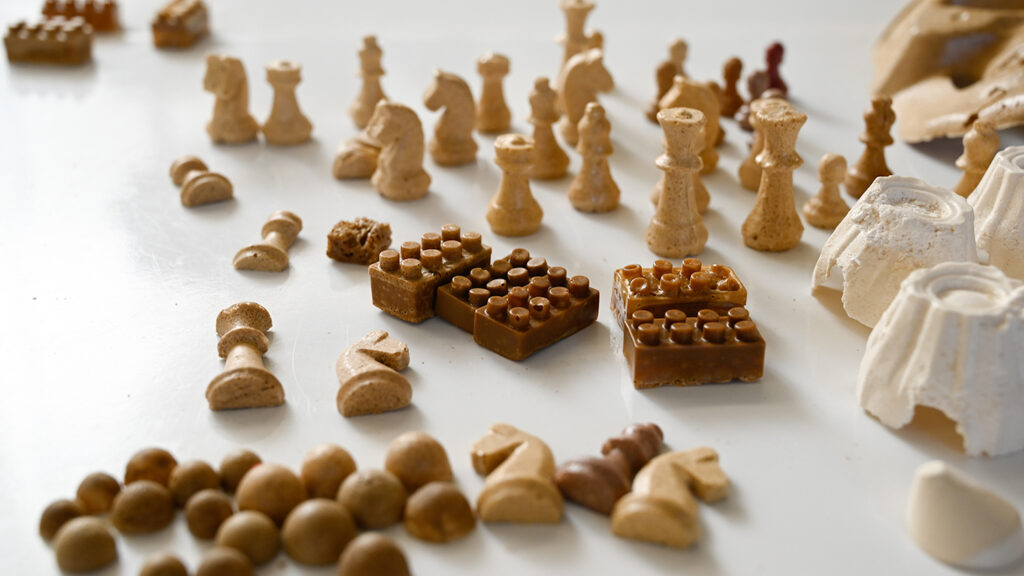
In an effort to address plastic pollution, researchers from around the world have developed biopolymer and fiber-based alternatives. These alternatives, however, require a lot of water, energy and chemicals to produce and therefore cost nearly 10 times as much as the material developed by Pal and Lucia.
Pal and Lucia have developed a production process that doesn’t require water. Instead, the researchers mechanically sieve, grind and mix sawdust with agro-residues to form a powder. The powder is then combined with a binder before it’s casted or molded into an item.
Also, because the researchers are utilizing sawdust, the production process is virtually zero-waste and zero-emissions. Sawmills and similar operations usually dispose of their leftover sawdust by burning it. This not only ends the life cycle of a valuable byproduct, but it also produces the greenhouse gas emissions driving climate change.
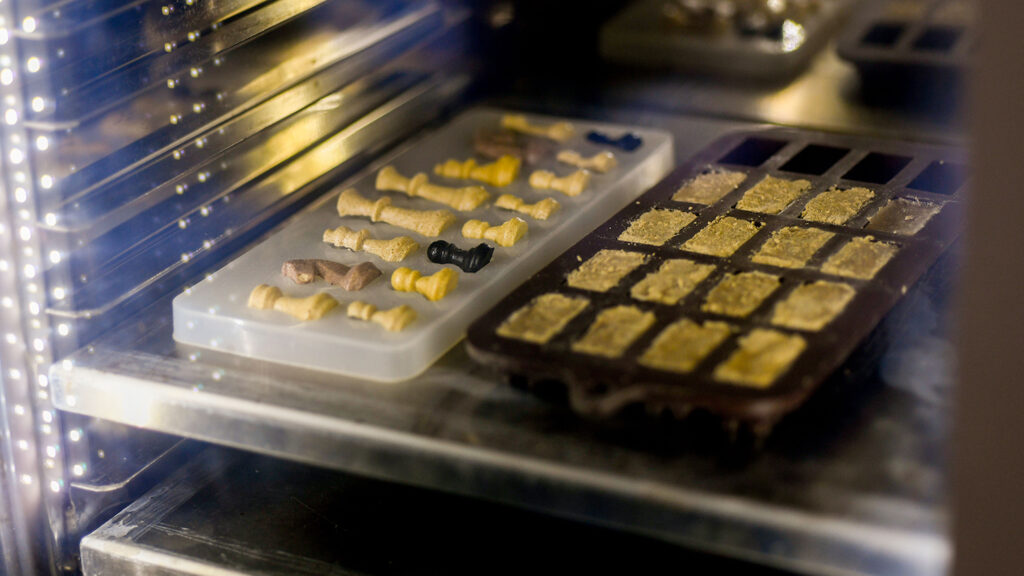
“Our research has focused heavily on environmental and economic sustainability,” Pal said. “We know this material is not only recyclable and environmentally compatible, but also biodegradable in saltwater. It will simply disappear over time and consequently provide nutrients to aquatic life.”
Pal added that the material also addresses social equity, reducing the impact of plastic pollution on marginalized communities worldwide. Research shows that plastic pollution is most highly concentrated along the coasts of low- and middle-income countries, which already have poor waste management systems.
Ultimately, as Pal and Lucia conduct pilot and commercial trials of their material over the next six months, they plan to further test its biodegradability and biocompatibility and to scale production for industrial partners. The researchers will also explore the use of 3-D printing in the production process, with the goal of eventually creating eco-friendly household items.
- Categories: